In 1908, Georg Simmel published his Psychologie des Schmuckes (Psychology of Jewelry). The way this great philosopher from Berlin described the egoistic and at the same time altruistic aspects of self-ornamentation is still compelling: “We adorn ourselves for ourselves, and can only do this by adorning ourselves for others,” is a central statement. Simmel categorized different types of jewelry using a scale, according to “how closely the individual types are related to the wearer’s physical personality.” Simmel placed “indigenous people’s intimate jewelry, i.e. tattoos” at the very bottom of the scale, metal and gemstone jewelry at the top, and the diamond at the very top. “Jewelry enhances or augments the aura of a person’s personality by radiating their charisma, as it were,” he wrote. This is why “shiny metals and exquisite gemstones have always been used as jewelry materials, and are ‘adornments’ in a much narrower sense than clothes and hairstyles, which, after all, are also ‘decorative’.” Even if contemporary jewelry designers use far more materials than “shiny metals and exquisite gemstones”, Georg Simmel’s thesis is still in line with the worldwide appreciation that diamond jewelry enjoys.
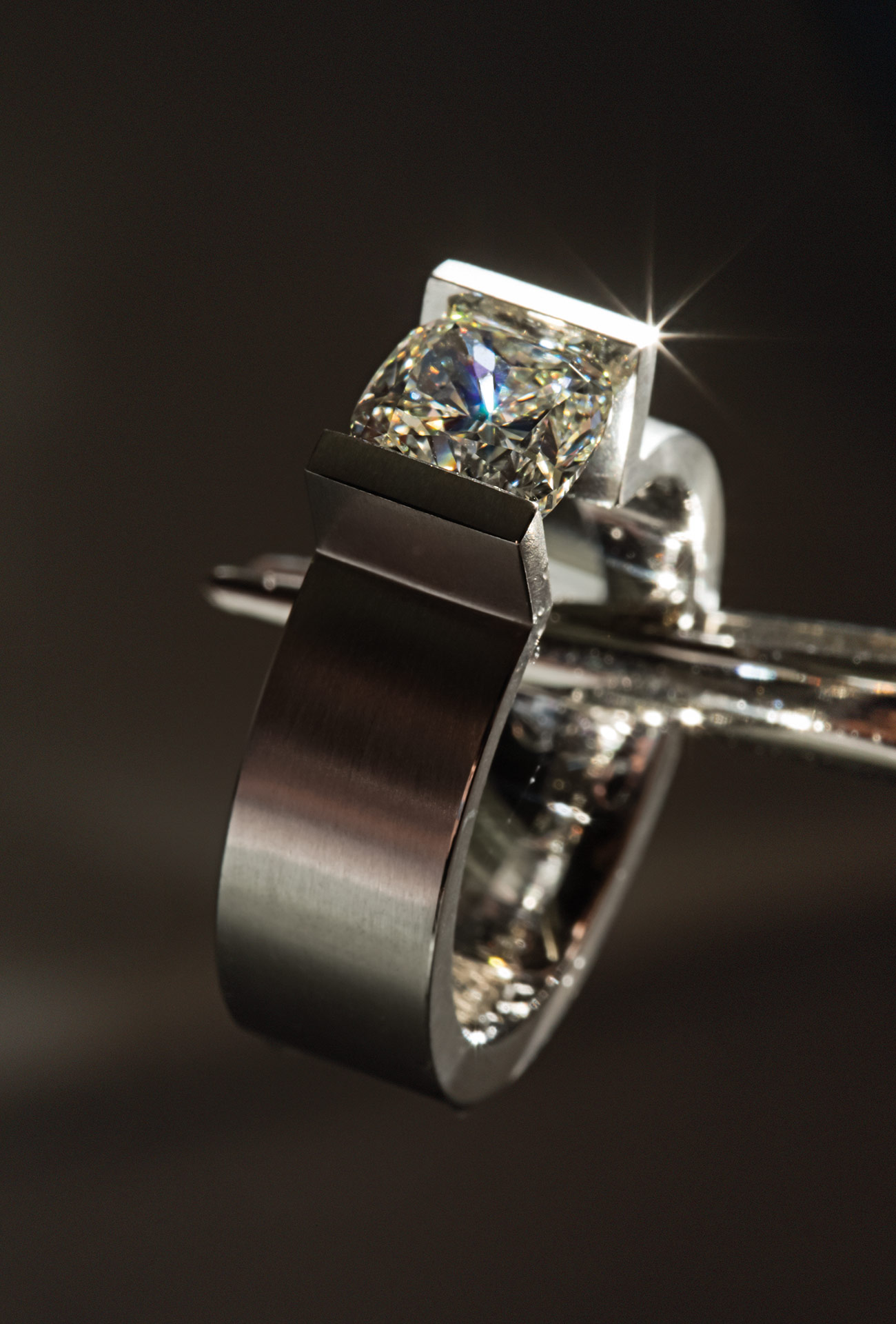
The result of the production process: a HighEnd C Niessing tension ring. 950 platinum, cushion-cut diamond
The diamond – called adamas (the unbreakable) by the ancient Greeks – is the hardest material that we know of. And it is, except for a few rare colored gemstones, also the most expensive gemstone. In a piece of jewelry, the stone is held securely by the traditional prong setting. When mounted in what is called a bezel setting, a diamond is completely surrounded by a metal ring, which, however, largely prevents the light from irradiating the lateral and lower facets. A diamond mounted like this is less brilliant. The majority of Niessing’s tension rings incorporate Excellence-cut diamonds, i.e. round brilliant-cut diamonds with 56 facets, plus a flat table. There are only two tiny points of contact where the diamond is held in place between the two ends of an open ring band. This means the exquisite gemstone can unfold its brilliance to perfection, and can also be experienced in its purest form.
The Niessing Tension Ring® was created in the late 1970s under the aegis of Ursula Exner, the company founder’s granddaughter. It was invented by the sculptor Walter Wittek, who inserted a glass disk into a steel sculpture, being held in place by the metal’s clamping force alone. The idea of placing a diamond instead of a glass disk between the ends of an open, hammered ring band to make it look as if it were hovering freely was born. But it was still a lengthy process to develop the technology required for creating the first tension ring. Because what’s essential for holding the diamond securely is a specific clamping force. It needs to be generated during the course of a precise hammering process to harden the precious metal, which is too soft in its original state.
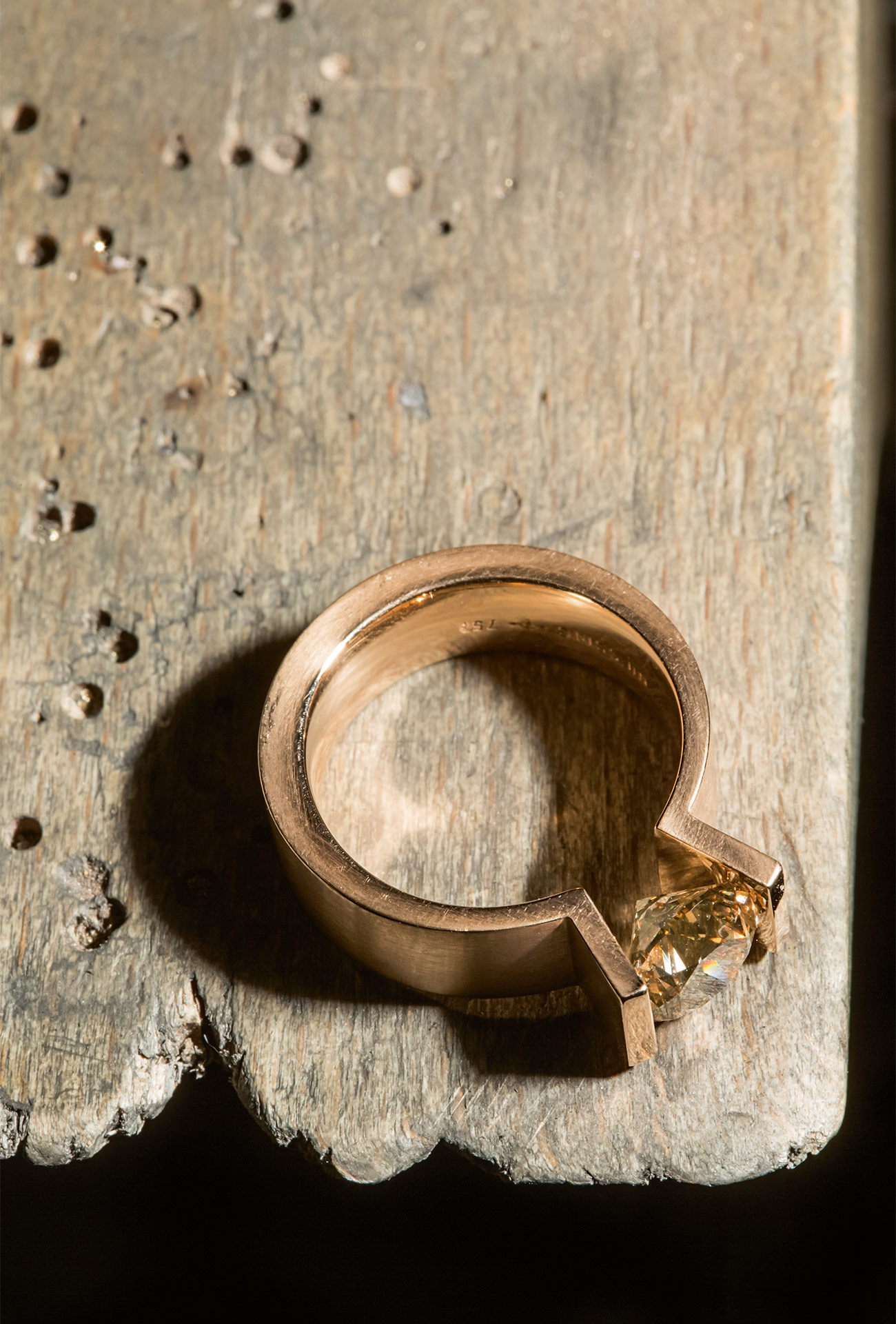
In 1981, the original edition of 99 pieces crafted from 950 platinum was launched on the market. The Niessing Tension Ring® became a worldwide success. It reflects a fundamental concept of modern design, i.e. that form follows function, has won numerous prizes, and has long since become a design classic. In 2001, the Niessing Tension Ring® was trademarked, and elevated to the status of a work of art. The jewelry manufactory in the Münsterland region has meanwhile developed many different ring shapes for its tension ring concept. The production process requires meticulous care and consummate skill – starting from the selection of the diamonds, the mixing of the alloys and the hammering process all the way through to mounting the diamonds and the polishing process. The following series of photos will give you an idea of how a tension ring is produced at the Niessing manufactory. We would like to thank Hans Verwohlt, Head of Product Development, who explained the fascinating technical details to us.
The Alloying, Melting and Casting Processes
The manufacturing process for a tension ring starts – as it does for any other piece of jewelry created at the Niessing manufactory – with the melting process. Niessing uses only recycled precious metals from a refinery to create the different gold alloys. The additions to the individual alloys are a company secret. First, the fine gold grains are melted together with the other alloy metals in an induction furnace at a temperature of up to 1100 °C. Then the liquid precious metal is poured from the crucible into a mold to form a bar.
Forming Processes, Annealing and Shaping
Developing unique gold colors as a result of special formulas is part of Niessing’s product philosophy. The traditional ring manufacturing method still practiced at Niessing involves elaborate forming processes. Repeatedly annealing the precious metal and quenching it in water eliminates molecular tension in the precious metal’s lattice structure. The “Tapered” tension ring is worked by hand into its final shape using a lathe – a work process that calls for the utmost concentration and a lot of experience.
Electroerosion, Milling and “Wedding”
The blank for a HighEnd tension ring is cut from repeatedly rolled platinum or gold plates. Rolling the plates in different directions serves to compact the precious metal and to obtain a high level of clamping force. The eroding machine is programmed individually to suit the size of the diamond concerned and the respective ring size. After the gemstone cutter has milled the “stone bed” into the metal – tiny grooves tailored to each individual gemstone to hold its edges –, the diamond is placed into it using gemstone tweezers, something that is affectionately referred to at the manufactory as “wedding the stone to the ring”. The left photo shows the “wedding” for a Niessing HighEnd tension ring made of rose gold, the right one is a Niessing HighEnd ring made of platinum.
Polishing and Cleaning
The Niessing tension rings are polished using various fabric buffing wheels and a micro-motor, which enables the user to finish the surfaces with all due sensitivity. Afterwards, the tension rings are cleaned with hot steam. The photo shows the Heaven tension ring, on the left made of platinum, on the right made of the new Rosewood alloy. Thanks to the wide variety of different models featuring different hues of gold or platinum, as well as to the different diamond sizes, each Niessing tension ring is a unique piece.
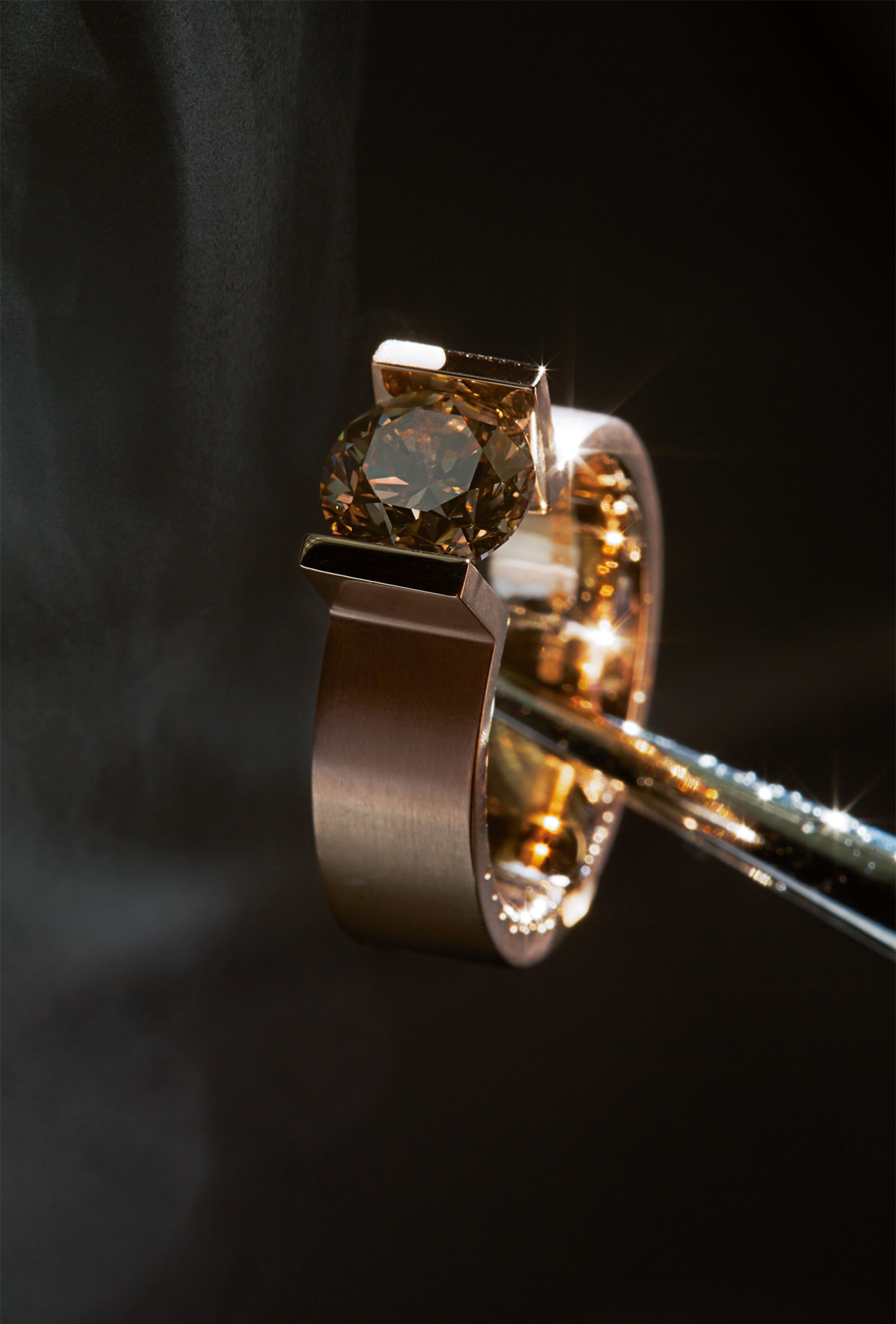
The finished product: a Niessing HighEnd tension ring. 750 rose gold, brilliant
Text Reinhold Ludwig
Photos Niessing
Translation Sabine Goodman
Appeared in ART AUREA 3–2016